This is Page 3 of 4 from the Ranger Boats Product Knowledge Tour (December 6, 2004) - Building Quality Bass Boats pages. Continuing on, we'll get into hull to deck assembly; rigging and some of the specialty areas of the Ranger Boats factory complex.
Building a Quality Bass Boat Pages
The Hull and Cap – Assembly
Rigging / Component Areas
CCBM – Another method to mold stronger, yet lighter fiberglass parts. Ranger’s exclusive closed cavity bag molding (CCBM) process eliminates emissions since it is performed in a closed silicon bag (right) under a vacuum. Ranger makes their own bags for CCBM. Pre-cut dry fiberglass reinforcement materials are fitted to a gelcoated mold. The materials are covered with the silicon bag. Hoses create a vacuum inside the bag and inject a measured amount of resin that saturates the fiberglass (applying in the picture below). Built-in vents in the mold aid in pulling resin throughout the entire part. The part cures inside the vacuum.
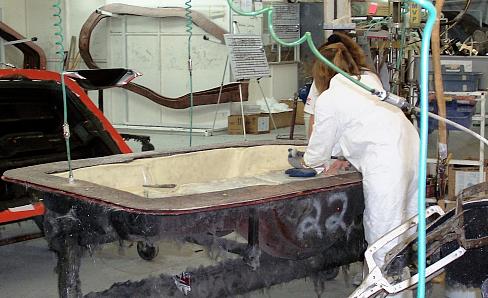
CCBM virtually eliminates fiberglass and resin waste. Hazardous emissions from curing are contained providing a cleaner and safer work place. You get a higher fiberglass to resin ratio too, which is how you get lighter, but stronger parts. Ranger uses CCBM to mold lids, trailer fenders, consoles, deck extensions, live wells, storage boxes and coolers.
A great deal of heat is generated from this process, which is the main reason Ranger only uses CCBM for the smaller parts other than the hull and deck.
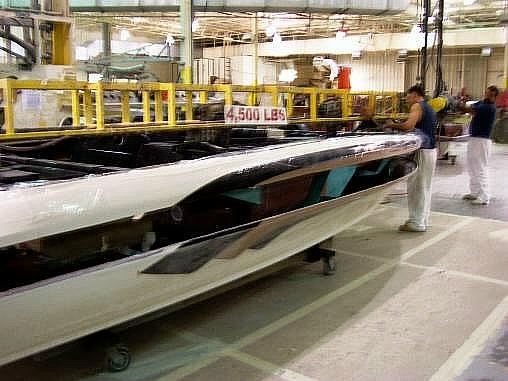
Ranger caps are bonded to the hull permanently with a 2-part epoxy agent. This picture shows a Z21 deck being lowered into its corresponding hull. Screws are used now in an improved process that keeps them from backing out.
The only way to remove a cap from a Ranger Boat is to cut it off in pieces. Another important part of Ranger’s one-piece unit philosophy you can count on even in the brutal waves of the Great Lakes. A solid bonded-together boat with all cavities filled with foam makes for a boat that will not come apart when the chips are down – the livewells are full of bass and the waves remind you of The Perfect Storm.
After the deck and floor are bonded foam is pumped in to fill the rest of any empty space for extra strength and soundproofing. Bubble trim is installed around box edges. This trim completes a watertight seal on the gelcoat edges for compartments and further dampens noise and vibration.
Carpet is then fitted to the boat and compartment lids from the same roll to ensure a color match. Ranger uses high-grade 20-ounce carpet that is stain-resistant and has special UV protection to reduce sunlight effects. The carpet backing is resistant to water and chemical damage. A water-based environmentally-friendly glue is used that is also moisture and chemical resistant. All Ranger’s carpet is now cut on the computerized laser cutting machine (see page 4) to the exact shape for each boat part. All the lids are carpeted together for each individual boat in a set that is keyed to each boat. Having the parts pre-carpeted in sets before they get to the boat now speeds up putting them in the boat and makes for a cleaner job.
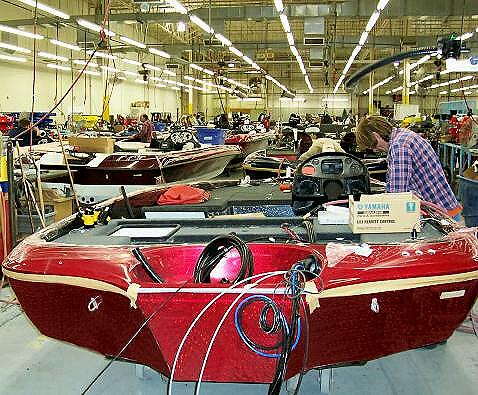
The Rigging room is next where each boat is mated with the wiring harness and components set (owner-specific bins) that matches what each owner has ordered for his or her new fishing rig. Plastic is taped around the cap so no scratches are put in the show room finish while all the cables, wiring (all wiring harnesses are custom-built for each individual boat) and components are installed as each boat works its way through the lines.
There are two lines that usually run the Comanche and Sport series. A line for the Fisherman series, and a line for Bay boats and Reatas. Adjustments can be made in the lines to handle an increase in demand for any type of boat. It takes 7 business days for each boat from the mold until it passes the ‘tank test’ at the end of the rigging room.
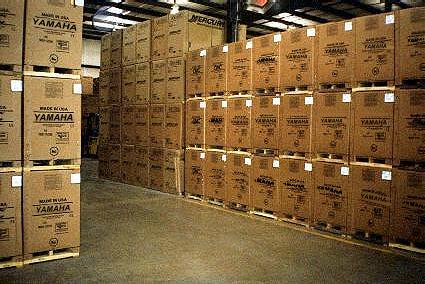
The old hyperventilation picture that is sadly no more. Thanks to faster computers and better inventory tracking, improved transportation and delivery, the big outboard stacks are gone. Now outboards come into Ranger in the models and quantity needed to meet the orders right about the time the transoms are ready for them.
The mountains may be gone, but there are still rows of big outboards and they keep coming in one right after the other.
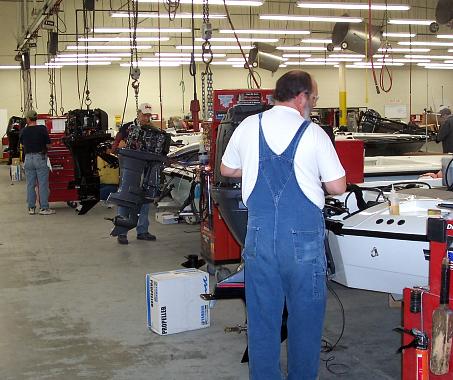
Motor mounting – near the end of the rigging room, each new boat has the outboard motor attached ordered by the soon-to-be owner. These technicians specialize in hanging every brand of outboard your heart desires (including my favorite – Yamaha!) customized however you’ve ordered them. All the batteries are off to the side being fully charged right before they are installed in your new boat. Also, the gas tanks are pressurized to 4 pounds to test for leaks. The technicians then make sure the motor has power so it will turn over using the fully charged batteries when you get it home and turn the key.
The new boat is then hoisted into a water tank for final inspection.
Please click page 4 for more pictures and info on the final water tank testing and other important parts of the final product including trailers and more of the high tech innovative processes developed by Ranger Boats over all its years of boat-building experience.